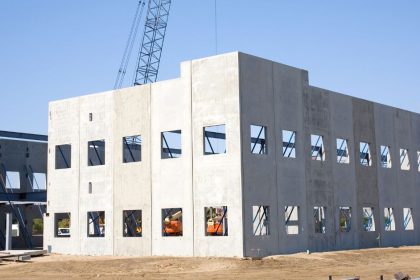
Precast concrete walls are often associated with premium quality and robust performance, making them a go-to choice in commercial, industrial, and even residential projects. Unlike cast-in-place concrete, precast elements are manufactured in controlled environments, ensuring consistent quality and faster on-site installation. However, many potential buyers wonder: are precast concrete walls expensive, and do they justify the higher initial costs?
In this guide, we’ll break down the factors that influence the cost of precast concrete walls, compare them to other wall materials, and explore how their long-term value often compensates for the upfront price. By evaluating both immediate and extended benefits, you can determine if precast is the right solution for your building or property needs.
Factors Influencing Cost
1. Customisation and Complexity
Design and Shape
- Precast panels can be customised in terms of texture, pattern, or size. Specialized designs or intricate finishes naturally drive up manufacturing costs.
- Complex architectural features require more detailed moulds and extended production time, which can add to the final price tag.
Panel Thickness and Reinforcement
- Thicker panels or those with heavy steel reinforcement (like double cages) cost more to produce. These might be necessary for walls that support significant loads or in high-security applications.
2. Installation Requirements
Transport and Handling
- Precast elements are delivered fully formed, so shipping large, heavy panels can incur higher transport fees.
- A crane or specialised equipment is often required to unload and position each panel accurately.
Site Preparation
- The site must be ready to accommodate a rapid install. Although labour hours on-site can be less than cast-in-place methods, you might pay more upfront for the necessary machinery and skilled operators.
3. Material Quality
Type of Concrete Mix
- High-grade concrete with additives or fibres might cost more but offers better durability and resistance to cracking.
- Some suppliers offer eco-friendly or lightweight mixes, which may further affect pricing.
Finishing Options
- Decorative surface treatments (e.g., acid-etched, polished, or coloured concrete) enhance aesthetics but add manufacturing steps.
- Special coatings or sealants can protect against moisture and staining, boosting longevity.
Comparing Precast Walls with Other Materials
While precast concrete walls can be pricier than alternatives (like masonry blocks or timber framing), they often deliver notable advantages:
- Masonry Blocks
- Pros: Lower upfront cost, widely available.
- Cons: Installation is labour-intensive, potential for inconsistent mortar joints, lower structural performance in certain high-load or seismic conditions.
- Timber Framing
- Pros: Less weight, simpler tools needed for construction.
- Cons: Susceptible to rot, termites, and requires ongoing maintenance or treatment.
- Cast-in-Place Concrete
- Pros: Familiar method, effective for large monolithic pours.
- Cons: Dependent on weather conditions, requires formwork setup and more on-site labour, which can extend construction timelines.
When measured across lifespan, strength, and maintenance, precast walls often emerge as a cost-effective choice over the life cycle of a building.
Long-Term Value of Precast Concrete Walls
1. Durability and Strength
- Extended Lifespan: Properly manufactured precast can last decades with minimal upkeep, thanks to consistent curing conditions in the factory.
- Resilience: Precast panels often boast impressive load-bearing capacity and are resistant to fire, rot, and pests.
2. Maintenance Savings
- Minimal Repairs: Precast’s uniform density and controlled curing reduce the risk of cracks.
- Less Frequent Replacement: Because panels are robust, you likely won’t face major repairs or replacements for many years.
3. Energy Efficiency
- Thermal Mass: Concrete helps regulate indoor temperatures, leading to potential energy savings in heating or cooling.
- Insulation Integrations: Modern precast can incorporate insulation layers within the panel, boosting R-values without extra installations.
4. Project Speed and Reduced Labour
- Faster Construction: Panels arrive on-site ready to install, minimising delays tied to weather or lengthy cure times.
- Lower Labour Costs Long-Term: Quick installation cuts workforce needs, although initial crane hire and skilled labour might be higher for a short period.
So, are precast concrete walls expensive? They can indeed have a higher upfront cost compared to some alternatives. However, factors like rapid installation, long lifespan, reduced maintenance, and exceptional structural integrity often justify that initial investment. When you evaluate the total life-cycle cost, precast walls frequently deliver robust value—particularly in settings where durability, appearance, and swift project completion matter most.
If you’re deciding whether precast is right for your project, consider its customisation potential, resilience, and energy efficiency. By factoring in both immediate budget constraints and the extended benefits of less maintenance and longer service life, you can make a confident choice that suits your property for years to come.